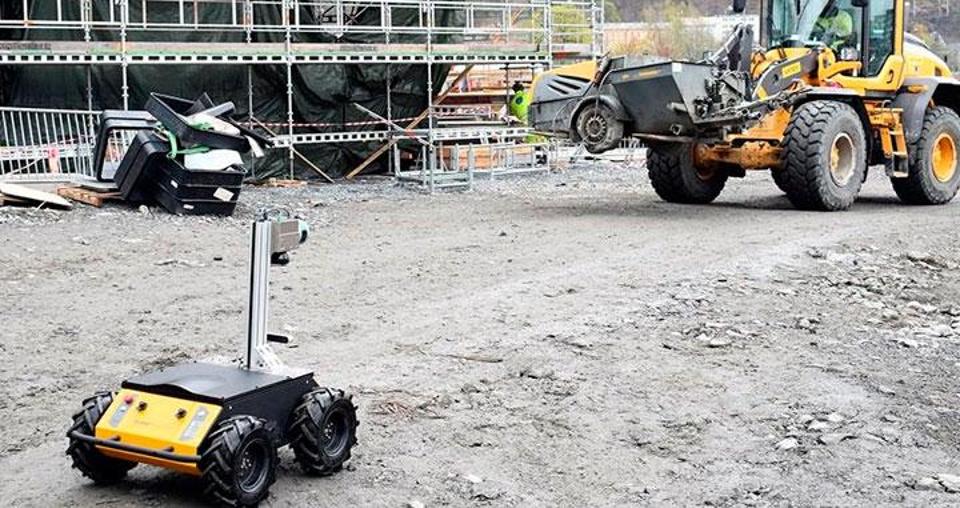
Robotics in construction will become a more common occurrence in the years to come, and could well … [+]
Scaled Robotics
The construction industry is in desperate need of an automated shake-up. With a serious skills shortage, limited resources, and outdated data collection practices, automation and robotics could save the industry from stagnation.
But digitization is coming for construction. Already robots are entering development sites, offering new capabilities that are humanly impossible, or simply providing the accuracy and continuity that are so crucial in the industry. Part one of this article will focus on robotics companies that are upgrading on-site capabilities to address the skills shortage that threatens to suffocate the construction industry.
Beyond digitization
Similar to the mining and oil and gas industries, construction has been sluggish when it comes to automation, although advanced technologies such as laser scanners and smart sensors are widely utilized on-site, and digitization is spreading through the industry. But just as these other industries have begun to embrace automation, construction is beginning to transition away from ineffective manual processes towards a more data-driven approach. “The construction industry is full of information stored on scraps of paper,” says Stuart Maggs, CEO of Scaled Robotics, “we can’t learn from previous work because we can’t compare notes—the ability to learn from data is incredibly valuable.” Digitization has grown more popular in construction, particularly Building Information Modeling (BIM) used to visualize construction sites and projects in 3D, but there are still simply not enough skilled workers on-site to implement plans effectively. As an industry that consists largely of dangerous, repetitive and unpleasant tasks, robots have a lot of scope to take some pressure off the construction industry and bring further digitization and innovation.
Scaled Robotics’ robot collects on-site data for their BIM software, navigating around the construction site using waypoints set in advance to drive semi-autonomously. This data is then dynamically added to a map, classified and color-coded according to its level of completion, and deviations such as warped beams are presented visually in a ‘heatmap.’ “It’s just impossible to do all this measurement, a surveyor would usually only check 5-10% of the elements,” says Maggs, “so this [robotics and digitization] allows you to easily verify that what you intended to build is actually being built.” Robotics in construction then is augmenting human labor by “giving the site manager extra abilities that they didn’t have before,” says Maggs, but it is also enhancing the digitization already within the industry, feeding much more granular data into more detailed models. As Maggs puts it, “we either innovate and bring in new abilities or the industry just stagnates and employment becomes even more of an issue.”
Getting down and dusty
The crucial juncture between digital models and the construction site is a sticking point however, and translating 3D modeling and data analysis into the real world has its challenges. “Nearly three quarters of US construction firms use BIM to resolve conflicts before work begins in the field,” says Dusty Robotics co-founder and CEO Tessa Lau, “however, transferring those construction blueprints out into the field still involves several manual steps, each of which introduces more risk of error.” Simple errors when starting a project can skew an entire building, due to inaccurate analog equipment (measuring tapes and spirit levels, for example), rounding measurements to the nearest whole number, or even ‘eyeballing’ lines and areas when planning or laying foundations. Robots can eliminate these errors by transferring data-driven blueprints directly to the site (Dusty Robotics’ FieldPrinter outlines digital plans on-site in ink, as opposed to hand-drawn chalk) but it also allows skilled laborers “to do their jobs more efficiently, with less wear and tear on the human body,” says Lau.
Interestingly, Lau refers to their robot as a “power tool… just like a forklift or an impact driver,” which seems to suggest that ‘tools’ (even if they are powered by data rather than manual labor) are more attractive that pure ‘robotics’ within the industry—regardless, “91% of US builders have difficulty attracting or retaining skilled labor” according to Lau, and she argues that “the only construction companies that will survive the next decade are those that embrace robotics.” Working with the workforce is critical then, as the only way for robotics to gain traction is to ensure that those working with the technology understand and accept it. “Every tech company has a responsibility to think about how the people being affected by this technology will react, and how it’s going to impact on their lives,” says Maggs. Perhaps presenting robotics as a (very powerful) construction tool, rather than something that could replace jobs, is the best way to ensure that adoption does not stagnate as soon as robots enter the workforce.
The perfect storm
Robotics has seen a massive increase in interest in almost every industry that relies on heavily process-driven or manual work. Construction could well be defined by these characteristics, and facing “increasing demand for housing and office space, and increasing building complexity due to environmental concerns,” means that automation is vital to the industry, says Lau.
As the industry warms up to the idea of using automation to augment existing workers, and those working on-site feel that robots “give them super-powers” says Lau, construction will change dramatically over the next five years. Just as manufacturing is now a completely changed industry from where it was only twenty years ago, the dull, dirty, and dangerous work that makes up a majority of construction could soon be strongly supported by robots.