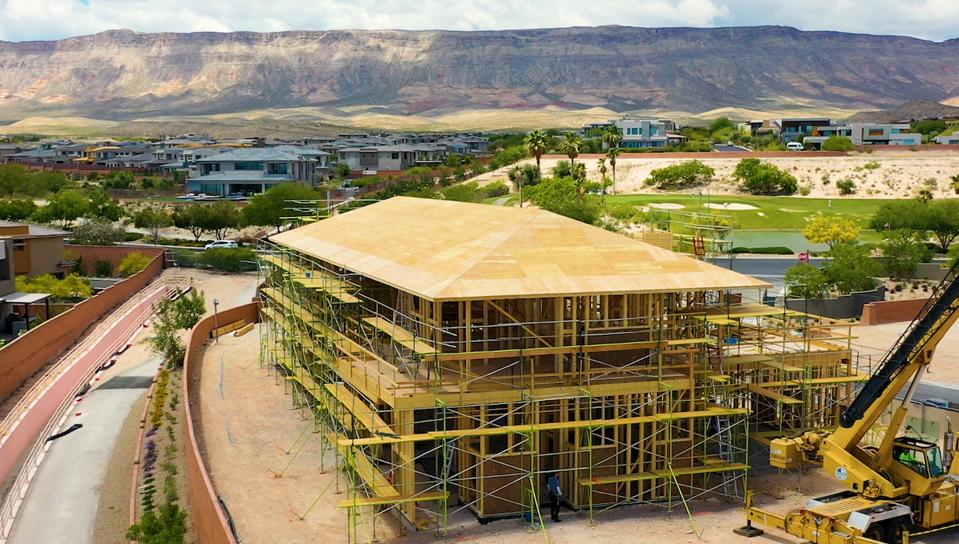
An aerial view of the project.
Woodside Homes
There has been very little innovation in the way new development homes have been built in America for years. Developers create a finite number of floor plans and present consumers with options for interiors, exteriors, finishes, etc. at a sales center. They put a price on all of it and buyers walk away with a semi-custom built home. This formula works and will likely work in the future. Or will it?
For over forty years, Woodside Homes has developed communities in California, Nevada, Arizona and Utah. While their most recent projects are becoming more energy efficient and finishes such as flooring more responsibly sourced, they realize that more needs to be done in terms of sustainable building for the long term.
In 2017, Sekisui House, which is Japan’s largest homebuilder, acquired 100% Woodside Homes. Sekisui is best known for building net-zero energy-efficient homes. Since 2008, they’ve built more than 43k of these properties, exceeding any developer in the world.
A concept house built by Woodside will showcase Sekisui’s innovations to the US market for the first time when it debuts at the 2020 Consumer Electronics Show (CES) and International Builders Show (IBS) in Las Vegas. This nearly 5500 square foot house has four bedrooms, five and a half bathrooms and a three-car garage.
A New Generation Of Buyers
Consumer expectations have changed dramatically in recent years. Previous generations were at the mercy of what the market had to offer. Social consciousness and corporate ethics weren’t something they considered when making purchases. But now buyers take all of this into account for every dollar they spend across the board, whether they are buying food, fashion, furniture or homes, which are the most expensive purchase they will ever make. Woodside doesn’t see this as a fleeting trend, but rather something they need to factor into their long term business plans.
Joel Abney, Vice President of Operations for Woodside Homes, shares that the concept home was designed to appeal to Generation X, who is coming into their largest buying power in upcoming years.
“Consumers are beginning to choose things with their dollars. They value spending their money in ethical ways,” he explains. “Traditionally homebuilders in the US as well as the rest of the world, struggle to meet those needs because it hasn’t necessarily been a forward thinking industry. Woodside has identified this as a need that isn’t being met.”
A New Concept
The concept home will serve as a springboard to integrate sustainability into Woodside’s current model. Many of the materials used to build Sekisui homes are made in a factory, customized to prevent construction waste. This includes the hardware, foundation system and floor system as well as some of the exterior materials. Each piece is accurately cut to the millimeter. The general standard is to cut to quarters of inches.
Sekisui homes use a specific post and beam structure called Shawood. This is nothing like a typical modular, boxy home, but rather offers a range of choices. “You don’t have to compromise on design for building efficiency,” Abney says.
The concept home was built four to five times faster than a traditional stick frame model would have been, even with the learning curve for the US crew.
The exterior of the house features a fire-resistant proprietary siding made of porcelain. In Sekisui’s Japanese sales centers, they even use a blowtorch to prove it. This material is also extremely earthquake resistant. Both of these benefits will particularly appeal to buyers in California and Nevada where fires and earthquakes can be major problems.
Holistic Design Means True Sustainability
“Everything is designed holistically in Japan,” says Abney. “All of the material is [sustainably sourced] to go specifically with the system.”
If the developer anticipates any waste will be produced, a recycling plan is created so the builder knows where it will go before the home is even built. This is a very sensible approach that should be taken into consideration for the American market. According to the EPA, in 2015, 548 million tons of construction and demolition debris were generated in the United States.
The Future
However, because a factory would need to be built, there are no stated plans to develop an entire community to these standards at the moment, explains Abney. “We are learning about the US and Japanese differences from a code and technical perspective. I think it’s going to influence our decisions in the future. Sustainability, energy efficiency and precision of the structural system, are all things we will apply to our future US business.”